Directional drilling in O&G comprises many different techniques like horizontal, multilateral, and extended reach drilling (ERD). These are common methods of enhanced oil recovery that help increase a downhole’s yield.
The drill string, drill bit, casing, and pipe all go down in a straight line in conventional oil and gas drilling operations. Any boring that does not go vertically down in a straight line is generally considered directional drilling.
Technically, when a driller aims 180 degrees away, it’s directional drilling. However, nowadays, it’s most likely that there will be a series of single or multiple carefully planned directional changes along wellbores.
Even in vertical wells, it is sometimes necessary to deviate to avoid a previously stuck pipe or geological formation before returning to the original path. Drillers use sidetracking techniques in such instances.
While directional drilling has been employed in oil and gas operations for over a century, technological improvements over the past few years have allowed turns, angles, and underground distances to be covered efficiently.
Companies like CNPS are working hard to engineer suitable ISO, OSHA, and API-compliant geological tools and equipment to boost safety and efficiency in the sector. Before you partner with us for our revolutionary solutions, here’s what you should know about directional drilling in O&G.
What Makes Directional Drilling So Valuable?
Directional drilling allows drilling multiple downholes through the same rig, resulting in minimal environmental impact or surface disturbance. These boreholes often extend over a mile down, with some going up to six miles at shallower angles.
A larger radius can be tapped in oilfields with dispersed deposits. This helps maximize the rig, which is an expensive asset. Crew and rigs have per-day rates that sometimes run into thousands of dollars. So a single rig working up to ten square miles is comparatively more cost-effective than having over a dozen vertical rigs, which might or might not tap into the same accessible reservoir deposits.
While geoscientists, seismic geologists, CAD experts, exploration engineers, and others involved in well planning team up to gain insights into the position and quality of oil and gas deposits in rock formations, sometimes Mother Nature organizes things differently.
Based on different surveys, experience, and well logs, they curate plans but cannot pinpoint where they could access the maximum resources.
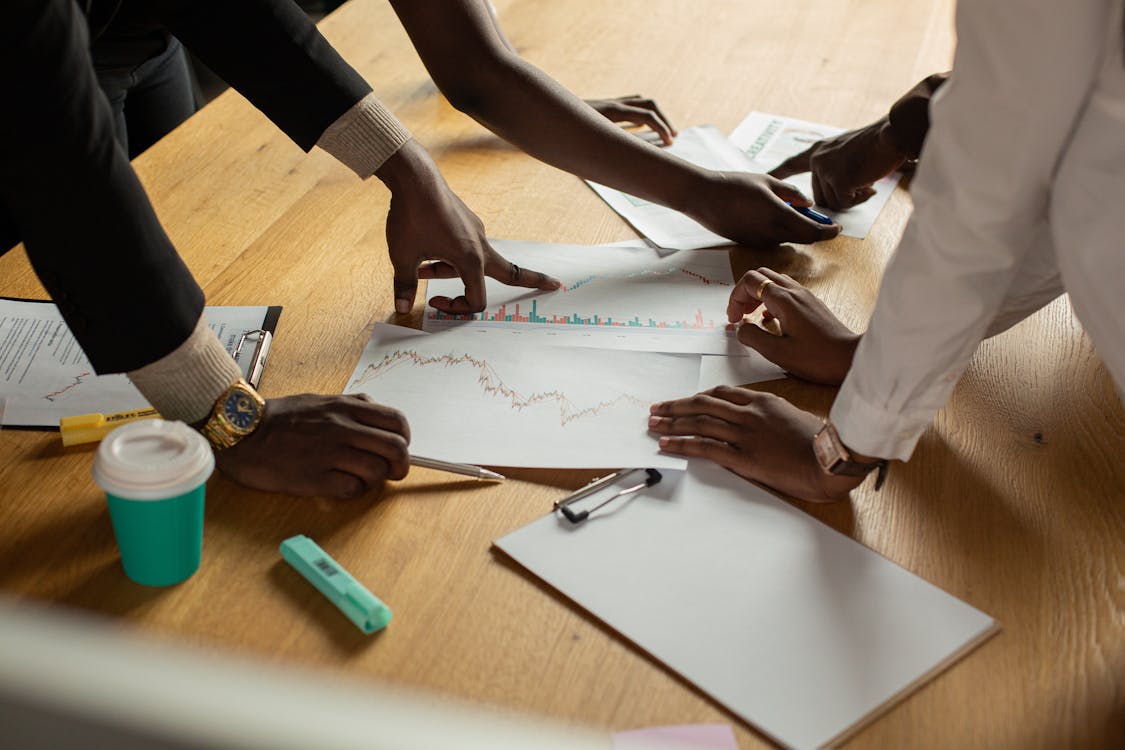
Drilling at an angle allows more of the reservoir to be explored since they tend to form between horizontal formations rather than vertical ones. Sometimes deposits don’t resemble reservoirs; they might be shale or oil-saturated sand. But directional drilling helps explore richer seams in the formations, making it especially valuable in shale.
From tough rocks to other factors making reservoirs inaccessible from above, such as the surface land being a mountain, town, special scientific interest area, or a natural reserve, many restrictive possibilities can be overcome by directional drilling.
Technical risks like deposits being found below fault planes or salt domes can also be reduced with horizontal drilling because it helps decrease pressure on equipment near fault lines while allowing the driller to avoid sale domes.
Other possibilities include reservoirs that may be connected in irregular patterns, hydrocarbon deposits settling in distinct pockets, or the reservoir extending diagonally down, resulting in the shallow ending providing minimal yields and the deeper end becoming hard to find vertically or drill.
In fact, with decreasing discovery potential for elephant reservoirs and increasing instances of oil and gas being found in irregular reservoirs, directional drilling is becoming critical every year.
Many companies create land rigs and drill horizontally under lakes or into the ocean to benefit from fewer risks and cheaper operations. Directional drilling also helps control ‘wild wells.’ Sometimes when a well is gushing after breaking through the blowout preventer, you need to cap it.
Depending on underground pressure, a second control well can sometimes be drilled to intercept at the same point where the first wellbore meets the oil or gas reservoir. When the directional well is completed, it’s pumped with kill fluid.
When the well pressure isn’t severe, the relief well also helps release gas so the original gusher can reduce in intensity, allowing gaining control. Water and mud are pumped in from a different angles to get the original well under control and back to the correct working order.
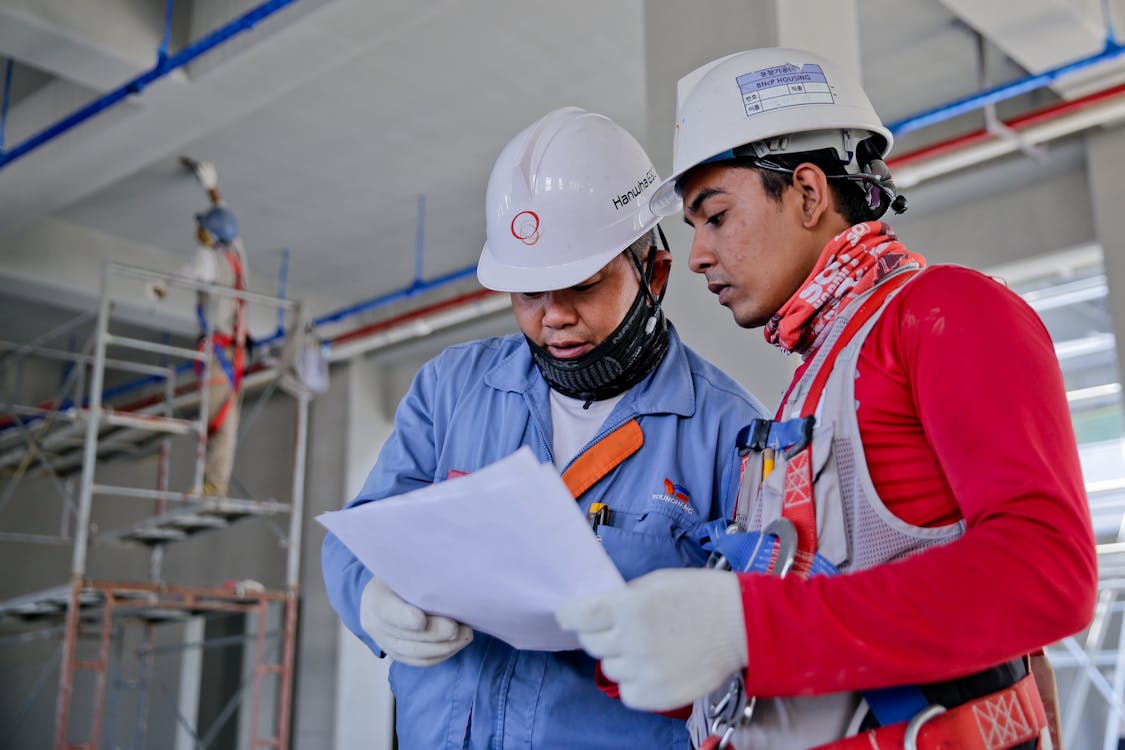
Find Geological Field Supplies at CNPS
Understanding the high risk and pressure involved in such operations, CNPS has stepped up to offer durable geological field supplies to reduce the likelihood of accidents and enhance safety and productivity during oil and gas extraction operations.
Our China-based company offers significant cost savings with its range of alloy OCTG products, GRE, GRP, RTP, and FRP piping systems, GRE casing solutions, mud logging equipment, EOR solutions, and geological field supplies.
We’re dedicated to delivering turnkey solutions for oil and gas, water, industrial, and marine & offshore. Our team possesses unrivaled precision capabilities and industry know-how to assist companies in all concerned sectors with diverse challenges.
Call us at +86 18354639099 for more information on our range of cutting-edge solutions for sustainable energy, mud logging, enhanced oil refinery, oil mining, production, and cementing.
You can set up a consultation with experts at CNPS or check out the information available online for geological supplies engineered with the latest technology to boost saving and enhance safety during risky operations.