Oilwell drilling represents the very heartbeat of the oil and gas industry, a complex and fascinating world where innovation meets the age-old quest for energy resources. This intricate process, blending engineering prowess with geological science, unlocks the earth’s rich reservoirs of oil and gas, fueling our modern world.
As leaders in providing innovative energy solutions, including advanced fiberglass pipes and GRE tubing, CNPS is at the forefront of this vital industry.
Mastering this art requires precision, advanced technology, and a deep understanding of the earth’s subsurface mysteries. With our extensive range of products, including cutting-edge mud logging equipment and reinforced thermoplastic pipes (RTP), we ensure the highest standards in every drilling project.
Therefore, this comprehensive guide offers an in-depth look into the oilwell drilling process, covering each critical stage from exploration to extraction.
At CNPS, we’re dedicated to enhancing every aspect of the oilwell drilling process. With our advanced technology and expertise in drilling mud solutions, fiberglass pipes, and renewable energy solutions, we’re here to support your projects’ success. Don’t hesitate to reach out to us at +86 183 546 39099 or [email protected] for assistance tailored to your unique requirements.
The Genesis of Drilling: Exploration and Site Preparation
Before a drill bit ever touches the earth, the journey begins with exploration—a scientific and strategic quest to locate potential oil and gas reserves. Geologists play a pivotal role, utilizing sophisticated technology like seismic surveys to map subsurface formations.
Advanced methods such as 3D and 4D seismic imaging allow for an even more detailed understanding of geological structures. Once a promising site is identified, rigorous environmental assessments are conducted, followed by careful logistical planning to establish access roads, water sources, and the necessary infrastructure to support drilling operations.
Rigging Up: The Assembly of the Drilling Rig
The drilling rig, an emblematic symbol of oilwell drilling, is assembled on-site. This mechanical giant, comprising several key components such as the mast, drill string, and blowout preventer, is designed to bore into the earth and safeguard the operation.
Critical to the rig is the power system, typically consisting of large diesel engines, which drives the drilling mechanism. Each rig component plays a vital role, with the drill bit and drill string penetrating the ground and the mud system, ensuring operational integrity.
The choice of the rig—whether a conventional land rig, offshore platform, or even an advanced automated drilling rig—depends on the location and environmental conditions of the drilling site.
The Drilling Process: Penetrating the Earth
Drilling commences, cutting through layers of rock to reach the hydrocarbon-bearing formations. This process is a delicate balance of power and precision, requiring constant monitoring and adjustments.
Advanced technologies, like rotary steerable systems, enhance directional drilling capabilities, allowing for more precise targeting of oil and gas reservoirs. Drilling fluid, or mud, circulated through the system, performs critical functions—it cools and lubricates the drill bit, carries rock cuttings to the surface, and maintains wellbore stability.
The composition of the drilling mud is carefully formulated to suit the specific geological conditions, with options ranging from water-based to oil-based mud.
Logging and Casing: Ensuring Integrity and Gathering Data
Once the target depth is reached, the next phase is logging and casing. Logging involves the use of specialized tools, such as mud logging sensors, to gather detailed data about the geological formations encountered.
Techniques like wireline logging, where electronic sensors are sent down the well, provide real-time data on aspects such as porosity, permeability, and hydrocarbon content. This information is crucial for evaluating the potential of the well and making informed decisions about its viability.
Following logging, a steel casing or alternative options like GRE casing are inserted to line the wellbore. The casing is cemented in place to prevent fluid migration, stabilize the wellbore, and ensure the well’s structural integrity. Advanced technologies, such as expandable casing, are increasingly being used to improve wellbore stability and reduce environmental impact.
Well Completion: Preparing for Extraction
Well completion is the process of making the well ready for production. This involves several steps, including perforating the casing in the hydrocarbon-bearing zone, stimulating the well to enhance flow, and installing production tubing and surface equipment. The design of the completion system is tailored to the specific characteristics of the reservoir.
This may include decisions on whether to use a single or multi-zone completion strategy and applying various completion technologies like gravel packing and frac-packing to optimize production and maintain well integrity.
In recent years, advancements in horizontal drilling and hydraulic fracturing have revolutionized well completion techniques, enabling access to previously unreachable reserves. Safety valves and downhole sensors are often integrated into the completion system to allow real-time monitoring and ensure control over the production process.
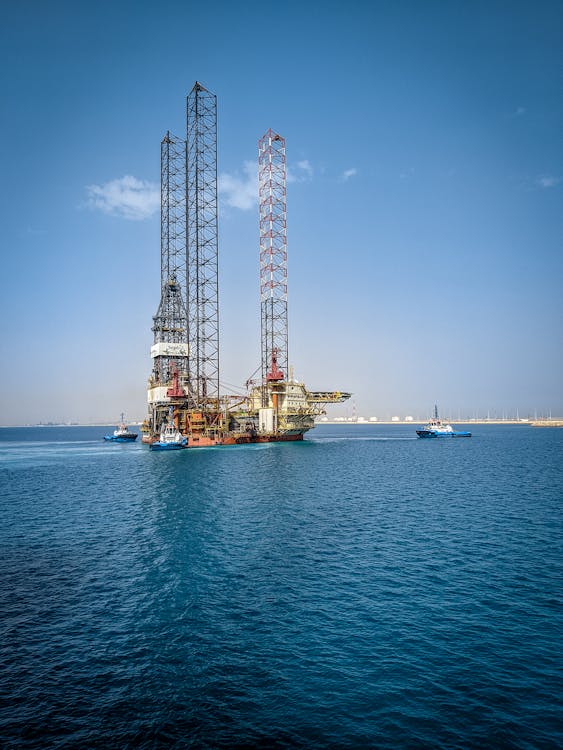
The Extraction Phase: Bringing Resources to the Surface
With the well completed, extraction begins. The production phase can last for decades, depending on the well’s productivity and the reservoir’s characteristics. Throughout this phase, careful monitoring and maintenance are essential to optimize production and ensure environmental and operational safety.
This includes the use of sophisticated techniques like artificial lift systems, including rod pumps, electric submersible pumps, and gas lifts, to enhance the extraction of hydrocarbons when the natural drive of the reservoir is insufficient.
During this phase, technologies such as seismic imaging and reservoir simulation models play a critical role in managing the depletion of the reservoir and predicting future production trends. Additionally, periodic workover operations may be necessary to repair or modify the existing well infrastructure to maintain or increase the output, adapting to changing reservoir conditions.
Advanced Technologies in Oilwell Drilling
Innovation continues to redefine oilwell drilling. Advanced technologies like horizontal drilling and hydraulic fracturing have unlocked previously inaccessible resources. Real-time data analytics, automated drilling systems, and enhanced oil recovery (EOR) methods are constantly evolving, pushing the boundaries of what is possible in oilwell drilling.
The application of machine learning algorithms and predictive modeling in drilling operations enhances decision-making and operational efficiency. Additionally, the development of more resilient drilling materials, such as fiberglass reinforced plastic pipes and GRE tubing, and innovative wellbore stability techniques are instrumental in reducing operational risks and environmental impact.

The Role of Sustainability and Safety
The oil and gas industry is increasingly focusing on sustainability and safety. Stringent regulations, environmental stewardship, and advancements in technology contribute to safer, more environmentally friendly drilling operations. The industry’s commitment to reducing its carbon footprint and protecting ecosystems is integral to its future.
This includes the implementation of green drilling practices, such as using biodegradable drilling fluids and employing waste management strategies that minimize environmental impact.
Additionally, ongoing research and innovation in carbon capture and storage (CCS) technologies present a promising avenue for mitigating greenhouse gas emissions during drilling operations.
The Future of Oilwell Drilling
The future of oilwell drilling is a tapestry of challenges and opportunities. As global energy needs evolve, the industry is adapting with a focus on efficiency, reduced environmental impact, and the development of renewable energy sources. The exploration and extraction techniques honed in oilwell drilling are also being applied in geothermal energy, demonstrating the industry’s adaptability and resilience.
Moreover, the integration of digital technologies such as AI and IoT in drilling operations is set to revolutionize well planning, drilling automation, and real-time decision-making. These advancements, coupled with an increasing focus on unconventional resources, such as shale and tight oil, suggest a dynamic and transformative future for the industry.
Oilwell drilling is a dynamic and essential component of the global energy landscape. From exploration to extraction, each step in the process is a testament to human ingenuity and technological advancement.
As CNPS, our commitment to providing advanced solutions and services ensures that we remain at the forefront of this ever-evolving industry. Specializing in oil and gas solutions, we offer a range of products, including fiberglass pipes, FRP pipes, GRE pipes, and reinforced thermoplastic pipes (RTP pipe), meeting various industry standards like API 15hr, API 15lr, and API 17j 15s RTP pipe.
Our expertise in GRE casing and GRE tubing, combined with innovative mud logging sensor technology, positions us as a leader in the field. Whether it’s through these cutting-edge solutions or our contribution to renewable energy solutions, we are dedicated to enhancing drilling efficiency and sustainability, contributing to a future where energy exploration and environmental stewardship go hand in hand.
For more information on our products and services, or to discover how CNPS can support your drilling operations with our range of energy solutions, including FRP fittings and flexible composite pipes, explore our website or contact us directly at +86 183 546 39099 or[email protected].
Together, let’s drill more sustainably.