Oil and natural gas extraction is a sophisticated operation that unfolds in three pivotal stages: drilling, completing, and producing. Each phase is integral to the successful delivery of hydrocarbons from beneath the earth to the end user.
This blog provides a detailed look into these processes, underscoring the advancements in materials and technologies that have revolutionized the industry.
Drilling: The Gateway to Energy Extraction
Drilling is the first step towards tapping into the earth’s energy reserves. This process involves creating a borehole that reaches the targeted reservoirs containing oil or natural gas. It’s a complex operation requiring precision, advanced machinery, and a deep understanding of geological formations.
- Technological Advancements in Drilling: Modern drilling operations leverage sophisticated technologies like rotary drilling rigs, which allow for deeper and more efficient penetration through the earth’s crust. Additionally, real-time monitoring systems, such as mud logging units equipped with advanced sensors, provide critical data on gas composition, formation pressure, and other vital parameters, enabling precise control over the drilling process.
- Materials Making a Difference: The use of durable materials like GRE and FRP pipes in drilling operations has significantly reduced the wear and tear on equipment. These materials withstand the harsh conditions encountered during drilling, including high pressures and corrosive substances, ensuring the longevity and reliability of the drilling infrastructure.
Enhanced Drilling Techniques
- Directional and Horizontal Drilling: Revolutionary drilling methods allow operators to drill wells vertically and at various angles. This is particularly advantageous for exploiting reservoirs situated in challenging locations or for reducing surface impact. Techniques such as directional drilling and horizontal drilling enhance the ability to reach and produce hydrocarbons more efficiently.
Innovations in Drilling Fluids
- Eco-friendly Drilling Mud: The development and use of environmentally friendly drilling fluids have become increasingly important. These biodegradable fluids help in minimizing the environmental footprint of drilling activities. Innovations in fluid technology also include the creation of fluids that can withstand extreme downhole pressures and temperatures, improving drilling efficiency and safety.
Advancements in Well Control
- Blowout Preventers (BOPs): A critical aspect of drilling safety is the use of advanced blowout preventers. BOPs are sophisticated mechanical devices designed to prevent the uncontrolled release of crude oil or natural gas from the well. They are essential for maintaining control over the wellbore in case of sudden pressure surges.
Drill Bit Technology Progress:
- Cutting-edge Drill Bits: The core of the drilling operation, the drill bit, has seen substantial advancements. Modern drill bits, made from materials like polycrystalline diamond compact (PDC), are engineered to last longer and drill more efficiently through various rock formations. This speeds up the drilling process and reduces the need for bit changes, thereby saving time and resources.

Completing the Well: Preparing for Production
Once drilling reaches the reservoir, the well must be completed to begin extraction. Completion involves several steps to ensure the well’s structural integrity and optimize the flow of hydrocarbons to the surface.
- Completion Techniques: There are various completion techniques, each tailored to the well’s specific characteristics. These include installing casing pipes, like GRE casing and FRP tubing, to reinforce the wellbore and prevent groundwater contamination. Hydraulic fracturing is another common technique, especially in unconventional reservoirs, to enhance permeability and increase hydrocarbon flow.
- Perforation Techniques: After the casing is placed, perforation guns are used to create controlled holes in the casing at the depth of the oil or gas reservoir. This allows the hydrocarbons to flow into the wellbore from the reservoir. The precision of modern perforation techniques ensures that only productive zones are exposed, enhancing the efficiency of hydrocarbon extraction.
- Enhancing Flow with Stimulation:
- Acidizing: This common stimulation technique involves injecting acid into the well to dissolve limestone, dolomite, and certain clay formations, creating pathways for oil and gas to flow more freely to the wellbore. It’s particularly effective in carbonate reservoirs, improving the permeability of the rock surrounding the well.
- The Role of Advanced Materials: Advanced materials play a crucial role in well completion. For example, fiberglass-reinforced plastic pipes and GRE tubing offer superior corrosion resistance compared to traditional steel, significantly extending the well’s operational life. Additionally, these materials can withstand high pressures and temperatures, making them ideal for the extreme environments of deepwater and high-pressure, high-temperature (HPHT) wells.

Producing: Extracting Value from the Ground
The final phase is producing, where oil and natural gas are brought to the surface, processed, and prepared for sale. This stage relies on the infrastructure established during the completion phase to extract, separate, and treat the hydrocarbons.
- Maximizing Production with Technology: Technologies like Electronic Submersible Pumps (ESPs) and Gas Lift Systems are employed to optimize the extraction of hydrocarbons. Smart wells equipped with sensors and automated controls can adjust production parameters in real-time, maximizing efficiency and minimizing downtime.
- Sustainability Through Material Innovation: As the industry focuses on sustainability, the use of environmentally friendly materials and processes has become increasingly important. For example, RTP and flexible composite pipes are used in water injection systems for Enhanced Oil Recovery (EOR) operations, reducing the environmental impact and extending the life of oil fields.
Enhancing Efficiency and Safety in Production
- Automated Monitoring Systems: The integration of advanced monitoring systems and IoT (Internet of Things) technology in production operations allows for continuous surveillance of well performance and environmental conditions. These systems facilitate the early detection of anomalies, preventing potential leaks and ensuring the safety of operations.
- Artificial Lift Systems Evolution: Beyond ESPs and Gas Lift Systems, the development of innovative artificial lift technologies, such as Hydraulic Pumping Systems and Plunger Lifts, offers tailored solutions for wells with varying characteristics and challenges. These systems are designed to enhance the extraction process, particularly in wells experiencing low natural pressure, ensuring a steady and optimized production rate.
Recovery Techniques for Enhanced Production
- Chemical EOR Techniques: The application of chemical Enhanced Oil Recovery methods involving the injection of surfactants and polymers to improve oil recovery represents a growing area of innovation. These techniques alter the fluid properties in the reservoir, increasing oil mobility and recovery rates.
- Thermal Recovery Methods: Thermal EOR techniques, such as Steam Assisted Gravity Drainage (SAGD) and in-situ combustion, are employed to extract heavy oils that are otherwise too viscous to be produced by conventional methods. These methods involve heating the reservoir to reduce the viscosity of the oil, facilitating its flow to the production well.
Looking Forward: The Future of Production Technology
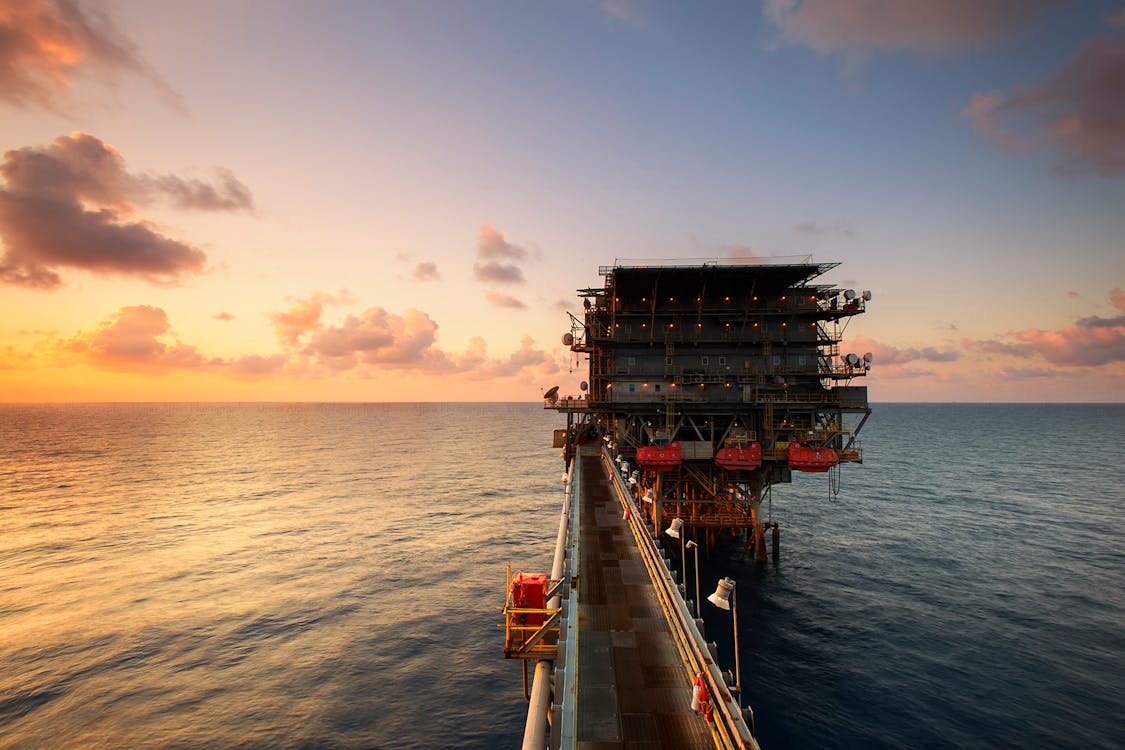
The Future of Oil and Gas Production
The oil and gas industry is continuously evolving, significantly influenced by the relentless pursuit of advancements in materials and technology. This journey is characterized by a deep commitment to enhancing efficiency, ensuring safety, and fostering environmental stewardship.
The integration of durable, corrosion-resistant materials such as fiberglass pipes, alongside the deployment of cutting-edge technologies across drilling, completion, and production phases, serves as a testament to this unwavering commitment.
- Advancing Materials Technology: The industry’s exploration into materials science has yielded innovations like fiberglass-reinforced plastic (FRP) and glass-reinforced epoxy (GRE) pipes, which offer remarkable benefits over traditional materials. These advancements promise increased longevity and reduced maintenance for oilfield infrastructure and contribute to safer and more environmentally friendly operations. The ongoing research and development in composite materials are expected to further revolutionize the sector, providing more efficient solutions and making it capable of withstanding the increasingly challenging oil and gas extraction conditions.
- Digital Transformation: The digitalization of oil and gas operations, by implementing technologies such as AI, machine learning, and IoT, redefines the industry’s landscape. These digital tools enable predictive maintenance, real-time monitoring, and production optimization, collectively enhancing operational efficiency and reducing environmental impact. The future will likely see a more interconnected and intelligent oilfield, where decision-making is informed by comprehensive data analysis and operations are streamlined through automation.
- Sustainability and Environmental Responsibility: As global awareness and regulations around environmental conservation tighten, the industry is accelerating its shift towards more sustainable practices. This includes minimizing flaring, optimizing water use, and implementing carbon capture and storage (CCS) technologies. Renewable energy sources are increasingly being integrated into operations to power remote sites, reducing the carbon footprint and leading toward a more sustainable energy mix.
- Collaborative Innovations: Collaboration between oil and gas companies, technology providers, and research institutions is fostering an environment of innovation where shared knowledge and resources are driving rapid advancements in technology and materials. This collaborative approach is crucial for tackling the sector’s most pressing challenges, from enhancing oil recovery in mature fields to ensuring the safe and efficient development of unconventional resources.
Connect With Experts
Understanding the complexities of drilling, completing, and producing from oil and natural gas wells is crucial for professionals in the field. With the right materials, technologies, and expertise, companies can enhance operational efficiencies, ensure safety, and move towards a more sustainable future.
Contact CNPS experts at [email protected] or +86 183 546 39099 for more information on advanced materials and innovative solutions. Our team is ready to assist you in exploring fiberglass casing, pipes, tanks, and renewable energy solutions that can revolutionize your operations.
From EOR technology to mud logging, cementing, and OCTG solutions, discover how CNPS can support your quest for operational excellence and environmental responsibility.Top of Form