In drilling operations, the management of drilling fluids, or mud, plays a vital role in maintaining wellbore stability, controlling pressure, and optimizing the overall drilling process. One of the most critical tools for monitoring and managing drilling fluids is the mud density sensor. By providing precise data on the density of drilling mud, these sensors help operators make informed decisions that enhance safety, efficiency, and performance.
This article explores the importance of mud density sensors and how they contribute to efficient drilling fluid management.
Understanding Drilling Fluid and Its Importance in Drilling
Drilling fluid, commonly known as “mud,” serves several essential functions in the drilling process:
- Wellbore stability: Drilling mud helps prevent the walls of the borehole from collapsing, keeping the wellbore stable.
- Pressure control: Mud density can be adjusted to balance formation pressures, preventing blowouts or formation damage.
- Cuttings removal: As the drill bit cuts into the earth, it produces rock fragments (cuttings). Drilling mud carries these cuttings to the surface, keeping the wellbore clean.
- Cooling and lubrication: The mud cools and lubricates the drill bit, reducing wear and extending the bit’s life.
To perform these functions effectively, drilling mud must have the correct density, which is where the mud density sensor becomes crucial.
The Role of Mud Density Sensors in Drilling
A mud density sensor provides real-time measurements of the mud’s density as it circulates through the drilling system. This information is critical for maintaining optimal mud properties, allowing operators to make adjustments that ensure the mud’s effectiveness in stabilizing the wellbore and controlling formation pressures.
Key Functions of a Mud Density Sensor
- Real-time monitoring: Mud density sensors continuously monitor the density of the drilling fluid, providing real-time data to the operators.
- Instant alerts for anomalies: If the mud density deviates from desired levels, the sensor sends immediate alerts, allowing operators to take corrective actions.
- Improving efficiency: By ensuring that mud density remains within optimal ranges, these sensors contribute to a smoother drilling process with fewer interruptions.
Benefits of Mud Density Sensors for Drilling Fluid Management
1. Enhanced Safety and Pressure Control
One of the primary benefits of mud density sensors is improved safety through better pressure control. The density of the mud directly affects the pressure it exerts on the wellbore. A density that is too low can result in well blowouts, while a density that is too high can cause formation damage.
- Well control: By keeping the mud density at the correct level, operators can maintain control over formation pressures, reducing the risk of blowouts.
- Quick response to changes: With real-time monitoring, the mud density sensor enables immediate responses to changes in pressure, allowing operators to prevent potentially dangerous situations before they escalate.
2. Optimized Drilling Performance
Maintaining the correct mud density is crucial for optimal drilling performance. If the density is off, it can affect the rate of penetration (ROP), lead to stuck pipe incidents, or cause excessive wear on drilling equipment.
- Efficient cutting transport: Mud density affects the ability of the mud to carry cuttings to the surface. A well-calibrated mud density sensor helps ensure that cuttings are efficiently transported, keeping the wellbore clear.
- Reduced downtime: By preventing issues like stuck pipe and formation collapse, mud density sensors contribute to fewer interruptions and reduced downtime during drilling operations.
3. Cost Savings and Resource Efficiency
Proper drilling fluid management is not only essential for safety and performance but also for cost efficiency. Using a mud density sensor allows operators to optimize mud properties, reducing the need for additional additives and improving resource usage.
- Minimizing mud waste: With precise control over mud density, operators can avoid the overuse of mud additives, saving on material costs.
- Extended equipment life: Maintaining the right mud density reduces strain on drilling equipment, extending its lifespan and minimizing maintenance costs.
4. Integration with Other Drilling Sensors
Mud density sensors are often used alongside other drilling sensors for comprehensive fluid management. For example, integrating data from a drilling mud flow meter and a sensor for drilling mud provides a full picture of mud properties, including flow rate, density, and viscosity. When combined with LWD drilling (Logging While Drilling) tools, these sensors offer invaluable insights into downhole conditions, allowing operators to make data-driven decisions.
How Mud Density Sensors Work
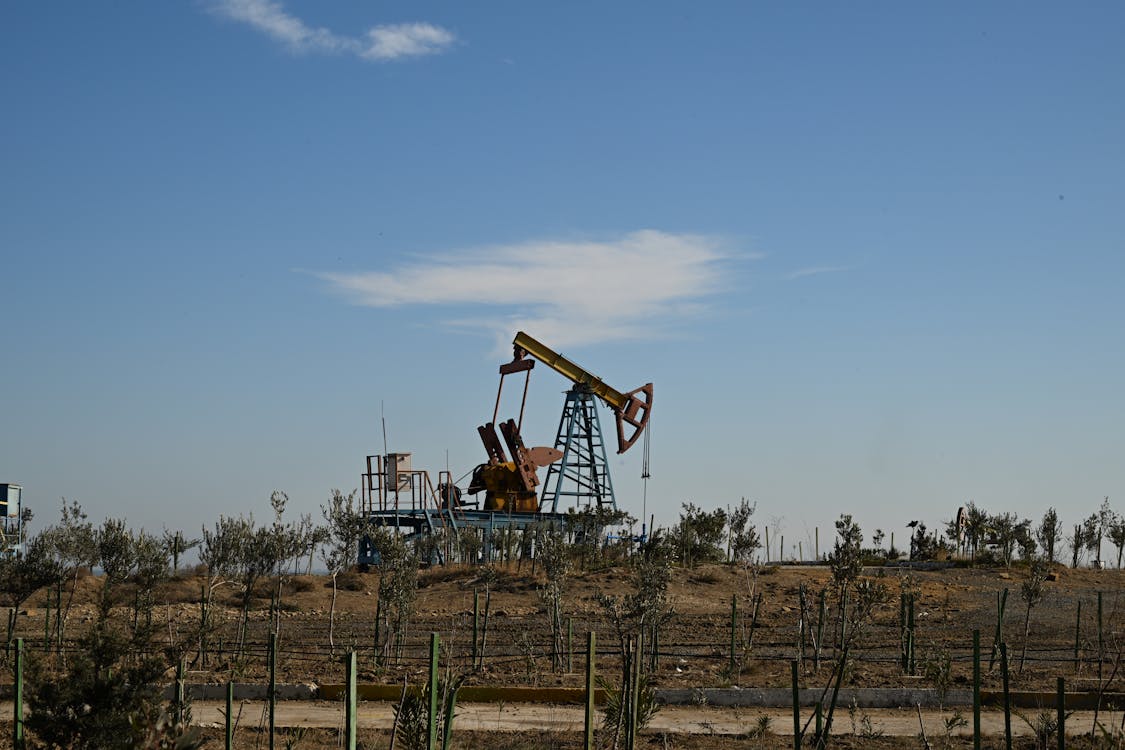
Mud density sensors typically use a vibrating element or other transducer technology to measure the density of the fluid as it flows through the system. Here’s a closer look at the process:
- Placement in the mud flow system: The sensor is positioned in the mud circulation line, where it can continuously measure mud density as the fluid flows.
- Real-time data collection: The sensor records density data and transmits it to the rig’s control system, where it can be monitored by the operators.
- Integration with mud logging tools: Mud density data is often integrated with other mud logging information to give a comprehensive view of the drilling conditions.
Best Practices for Using Mud Density Sensors
1. Regular Calibration and Maintenance
For a mud density sensor to provide accurate readings, it must be properly calibrated and maintained. Regular checks ensure that the sensor operates correctly and continues to provide reliable data.
- Routine calibration: Calibrate the sensor periodically to prevent measurement drift and ensure consistent accuracy.
- Maintenance and cleaning: In drilling environments, sensors can be exposed to abrasive particles and harsh conditions. Regular cleaning and inspection help extend the sensor’s lifespan and maintain its functionality.
2. Integration with Drilling Analytics Systems
Mud density sensors can provide even greater value when integrated with drilling analytics systems. By analyzing density data alongside other parameters, such as mud flow rate from a drilling mud flow meter, operators can make more informed decisions and improve drilling performance.
- Centralized data monitoring: Integrate the mud density sensor with other monitoring tools in a centralized system to allow operators to track multiple parameters simultaneously.
- Predictive analysis: Data from the mud density sensor can contribute to predictive models, helping operators anticipate and mitigate potential issues.
3. Operator Training and Awareness
Accurate sensor data is only useful if operators know how to interpret and act on it. Providing training on the use of mud density sensors and the importance of mud density in drilling operations can maximize the sensor’s benefits.
- Training on mud management: Train operators on the role of mud density in drilling performance and safety, emphasizing the need for vigilance.
- Quick response protocols: Establish protocols for responding to mud density anomalies, ensuring operators take prompt action when necessary.
CNPS’s Mud Density Sensor Solutions

At CNPS, we understand the critical role that mud density sensors play in drilling fluid management and overall well control. Our sensors for drilling mud solutions are designed to provide accurate, real-time density measurements that support safer and more efficient drilling operations.
In addition to our high-quality mud density sensors, CNPS offers a range of equipment to support drilling fluid management and optimize drilling performance:
- Drilling mud flow meter: Our drilling mud flow meter allows operators to monitor the flow rate of drilling mud, ensuring circulation remains within safe parameters. This is essential for maintaining well control and preventing issues like blowouts.
- Sensor for drilling mud: Our sensor for drilling mud provides vital measurements of fluid properties, contributing to effective drilling fluid management and improved operational control.
- LWD drilling tools**: We offer a selection of LWD drilling tools that provide downhole data, enhancing situational awareness and supporting decision-making during drilling operations.
Why Choose CNPS for Your Drilling Needs?
CNPS is committed to delivering high-quality oil and gas solutions that enhance drilling safety and efficiency. Our products are designed to meet the demanding conditions of drilling environments, providing accurate, reliable data that helps operators optimize their operations.
Explore our full range of products, including our advanced mud density sensors and drilling mud flow meters, and see how we can support your drilling projects.