Mud logging is an important technique for inferring lithology in the gas and oil exploration sector. It refers to the method where a borehole is drilled, and rock chips are brought to the surface by circulating drilling mud to analyze the sample, which is why it’s also widely known as surface logging.
The name takes after the fact that mud is one of the most commonly used mediums for surrounding drilling operations. However, the term is becoming outdated as technology progresses.
During the process, geologists identify downhole lithology, monitor gases entering the drilling mud stream, mark hydrocarbon positions according to depth, and create well logs. All of these help detect the presence of geothermal areas, natural gas, and oil. Additionally, it also helps geologists avoid drilling in the wrong spots while pinpointing the most productive strata.
Mud logging is typically done when a company decides to drill testing wells on a particular spot intending to harvest natural resources beneath the ground. Once multiple or a single well is drilled, the extraction process begins.
It requires specialized and often very expensive equipment to ensure success when getting a sample. Companies like CNPS provide geological tools and supplies and mud logging equipment for the task.
The Objectives of Mud logging
Mud logging primarily strives to identify potential hydrocarbon-rich formation sites for drilling. The data obtained from mud logging solutions is used to place, build, and maintain drills successfully.
The domain of mud loggers ranges from the shale shakers to the drilling floor outside the mud logging unit. The shale shaker produced gas and formation cuttings through the drill bit to be transported to the exterior in the drilling fluid.
Mud loggers stop over the shaker periodically to collect cuttings for microscopic analysis. A suction line between the mud logging unit and the shaker carried hydrocarbons from the trap to the hotwire detection system of the unit.
The visits help procure critical information exchanges between drillers and mud loggers who produced concise accounts of drilling activities using basic surface measurements. Rate of penetration, lithology, and gas measurements provide reservoir potential indications for decades.
Mud loggers gain valuable insights about formations from wells before the advent of LWD and MWD, where well trajectory, formation characteristics, and drilling conditions conspired against deploying wireline mud logging tools.
The technology has now advanced, and mud loggers can get glimpses of near-bit conditions through LWD in real-time. But adverse well bore conditions can impede the use of downhole mud logging tools.
In these scenarios, mud logging continues to give insights to operators regarding the well’s producibility. The log also provides operators with prompt indications of zones that demand special attention.
Another crucial objective of mud logging is to prevent explosions, blowouts, and catastrophes by monitoring the pressure, temperature, and other levels around the well bore. Estimating porosity and pore pressure, as well as the drilled formation’s permeability and keeping records of the drilling parameters, are also included in mud logging tasks. The goal is to ensure economically optimized, efficient, and safe operations.
What Do Mud Loggers Record?
Mud logs comprise the entire geological records of the drilling site along with many essential parameters like mud characteristics, drill time, and evidence of gas and oil. Indication of gas or oil is known as a show, so when loggers spot either of them in the samples, they record it in the log.
Other data about types of rocks and minerals, porosity, pore pressure, and the permeability of the surrounding formation are also recorded. Gas levels, pump pressure and rate, flow-line temperature, hydrocarbon evaluation, mud weight and density, and drilling rate information is also included.
Mud logs were manually written in the past, but technological advancements have enabled computer and cloud input and storage, making future analysis easier. Additionally, the scope of mud logging solutions has also broadened with time. Cutting-edge sensors are now able to bring more data into mud logging units, expanding diversity from weight-on-bit to gas chromatographs and pit mud level indicators.
Surface logging equipment now tracks visual carbon indicators, lithology, ROP, individual hydrocarbon compounds, total combustible gas in mud, and many other drilling parameters. The information monitored at the hub with rig sensors and drills makes mud logging solutions a critical source of information for geologists, drillers, and O&G companies.
Mud loggers monitor gas trends developing during drilling. These are integral to the assessment of mud balance and the indication of potentially over-pressured formations. Loggers carefully track the parameters to promptly warn the drillers and workers at the office so they can shut the well or mitigate the issue by adjusting the drilling fluid density.
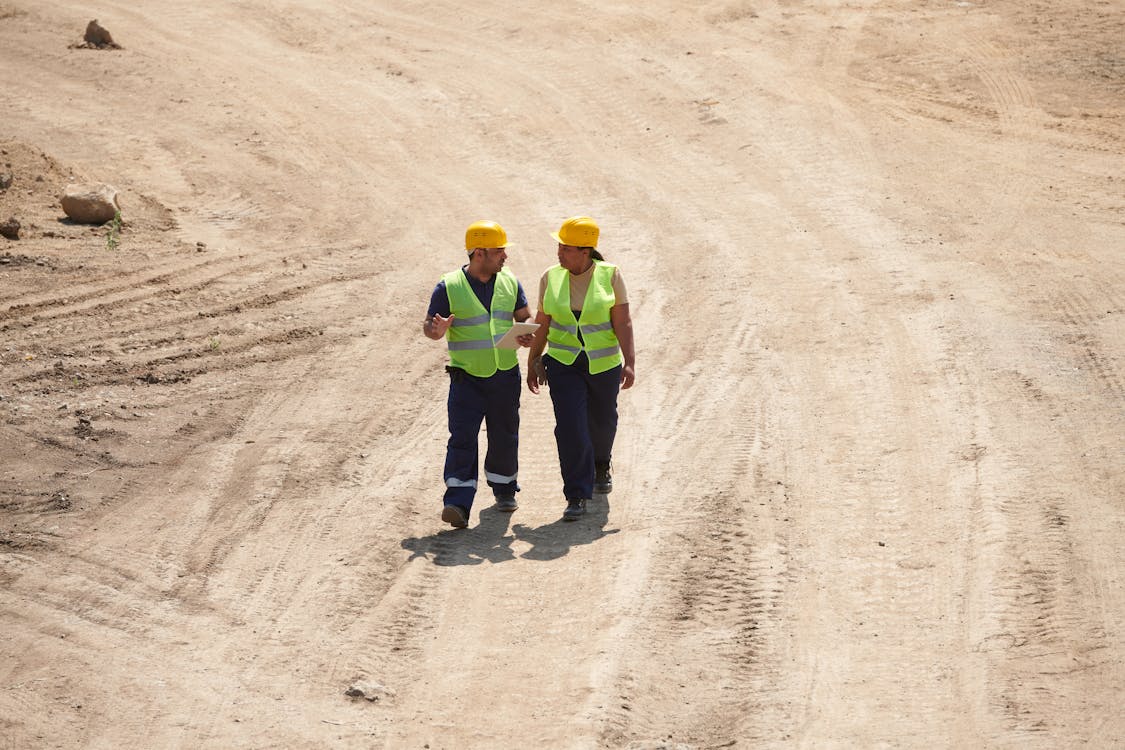
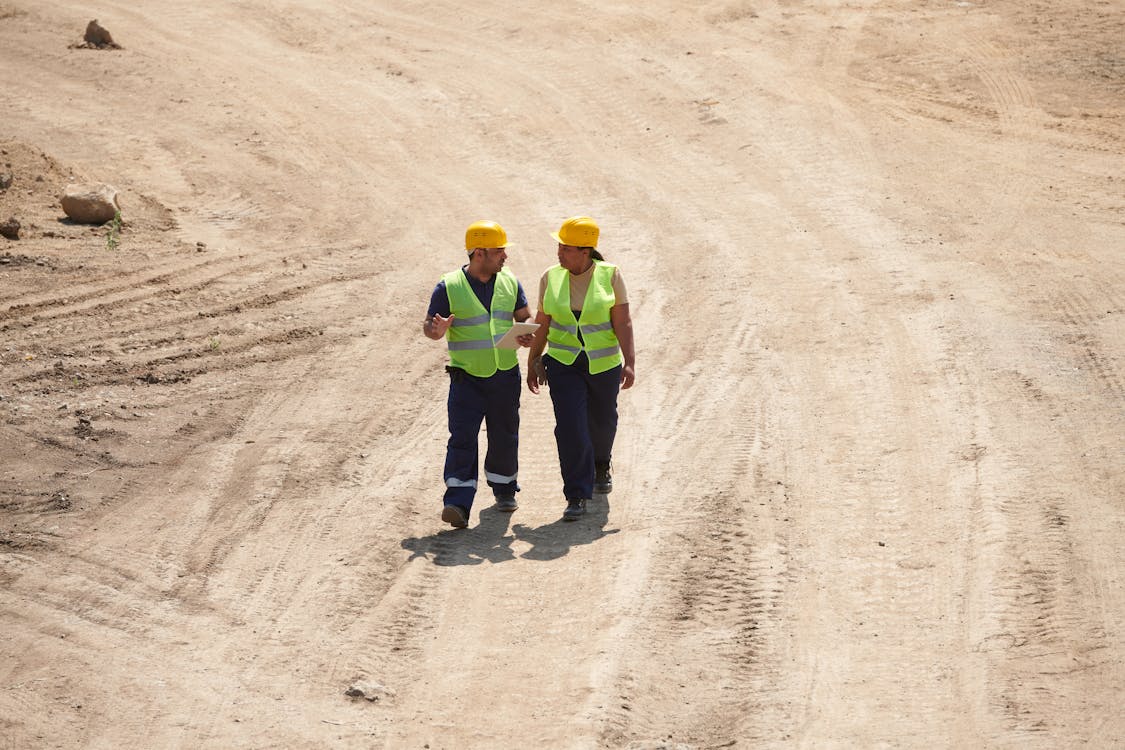
How Do Mud Loggers Obtain the Data?
Skilled mud loggers obtain insights from cutting samples taken at several points in the well bore’s surrounding area. This includes the possum belly and suction pit. They measure them at regular intervals—a challenging task, especially when continuous drilling is required. The samples are subsequently analyzed periodically as well.
The mud’s temperature, pressure, and gas levels are monitored constantly to prevent mishaps. The data acquisition requires sophisticated equipment for analyses. Since reliability and safety are important factors during such operations, CNPS offers a range of mud logging equipment and geological field supplies to add productivity and efficiency to the process.
The Drilling Process: A Brief Overview of
Surface logging heavily relies on mud circulation to carry the fluids and formation cuttings to the surface. Mud pumps draw the fluid with high pressure from surface tanks to direct it downhole through reliable drill pipes. The mud exits the drills via valves at the bit’s face.
Mud is forced upward because of the pump pressure through the annual space between the casing and drill pipe, causing it to exit at the surface via a flow line near the blowout preventer. It passes over a mesh screen that vibrates near the shale shaker. Here, the formation cuttings and liquid mud get separated. It falls back into the mud pit through the screen before being pumped back into the well.
When the bit drills through the subsurface, gas, oil, water, and rock grind up to be carried to the surface by the drilling mud. When and what arrives at the surface are both integral to the success of the mud logging process. The timing of arrival and material type are influenced by lithology, pressure, and drilling practices to varying degrees.
Besides bringing rock chips to the surface, the drilling muds lubricate and cool down the drill bits. It also controls the well’s pressure. Let’s look at it in a bit more detail.
Cuttings are created during drilling, and they rarely pose issues until the drilling is halted because the drill bit requires replacement or any other problem. In this scenario, drilling fluids don’t get used, and the cuttings fill the hole again. Drilling fluids can be used as suspension tools to prevent this from occurring.
Drilling fluid is integral to drilling projects in the oil and gas fields. It’s used in petrochemical, engineering, and heavy mining projects such as oil and natural gas extraction.
Petrochemical and engineering experts define drilling fluid as a high-density, thick, and extremely viscous liquid used during oil and gas drilling operations. They are manufactured according to ISO 10416–SIS, ISO 10414-2:2011, API RP 13B-1, and API RP 13I.
Be it oil-based, water-based, or gel-based—the fluid is essential to clean the drill bit’s hole and cool down the heat from the bit face. It prevents the influx of formation fluids and increases well bore stability.
The drilling fluid’s viscosity increases as the movement reduce, enabling the fluid to maintain a liquid consistency during drilling. It then turns into a solid substance once the drilling stops. Until the drill is inserted again, cuttings remain suspended in the well. The gel-like substance transforms into a liquid again when the drill is started.

The drilling fluids also help control the well’s pressure by offsetting the rock formations and hydrocarbon pressure. The density is increased by adding weighting agents to the drilling fluids and, simultaneously, the pressure on the well’s walls.
Drilling fluids also aid rock stabilization. Many special additives are used to ensure the pores don’t get clogged, and the fluids aren’t absorbed by the rock formations.
Many variations of the basic freshwater and clay mixture have been developed. Some well-known ones are based on diesel oil, mineral oil, saltwater, nitrogen, foam, mist, and polymers. Each one has particular properties to deliver superior performance in challenging drilling environments.
Each also requires special adjustments when it comes to surface logging. Certain require special sample rinsing techniques, while others rely on custom sampling procedures.
Properties of a Good Drilling Fluid
While the choice of fluid—synthetic, oil, salt, or freshwater- depends on the requirements of wells, several additives are also involved. OSHA highlights weighting compounds, such as barium sulfate, enhance the mud’s density to equilibrate the pressure between the formation and well bore when drilling through certain pressurized zones.
Zinc carbonate, aluminum bisulfate, iron oxide, zinc chromate, and other corrosion inhibitors can protect equipment and pipes. Iron lignosulfonates and dispersants help break up solid clusters into tiny particles, enabling the fluid to carry them. Surfactants emulsify and de-foam the mud, and flocculants group the suspended particles together to remove them from the fluid at the surface.
Fluid loss inhibitors limit the loss of drilling mud to high-permeability or under-pressurized formations. And biocides help reduce drilling mud scouring and prevent bacteria.
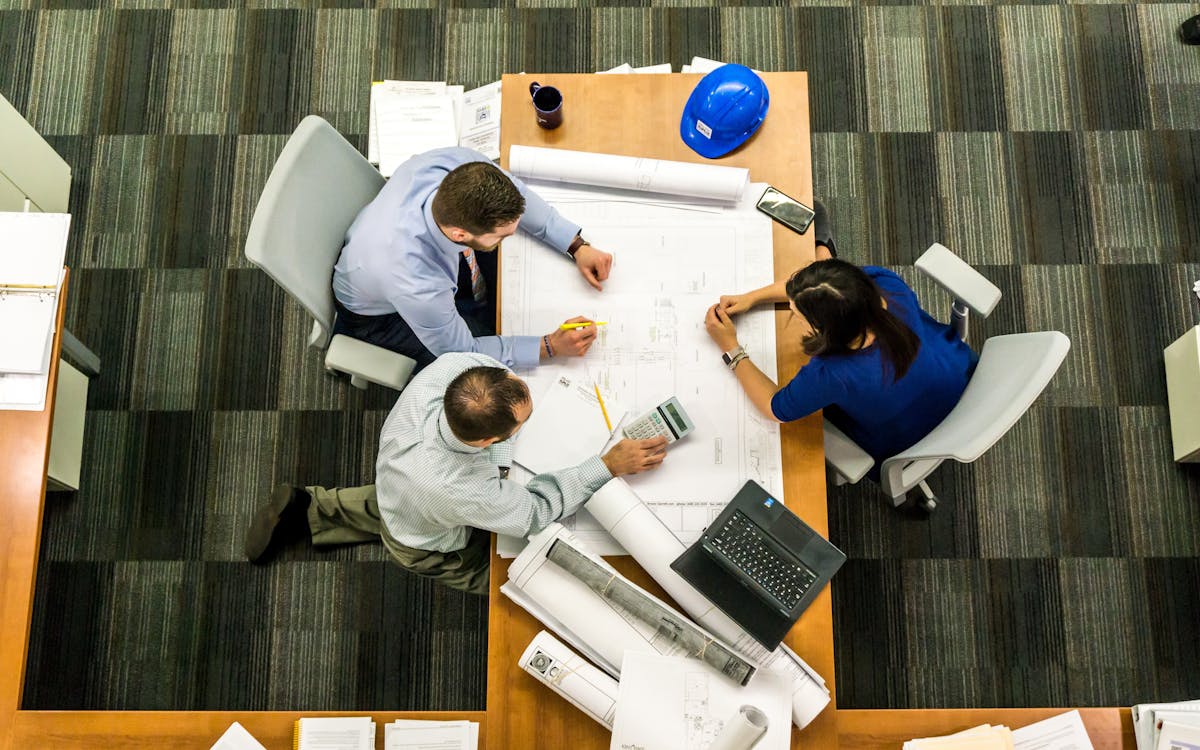
The Eco-Friendly Side of Mud Logging
Mud logging is important for optimizing process productivity, safety, and efficiency during petro extraction, water well drilling, gas mining, and mineral exploration. However, surface logging is quite beneficial for the environment despite the drilling tasks. It helps find scarce fossil fuel resources more efficiently without disrupting the ecosystem like traditional drilling that involves trial and error.
Many companies are shifting to geothermal technology to find renewable fuel sources through mud logging. The equipment helps detect the existence of geothermal energy in the region, allowing it to tap into the water and bring it to the surface. It can power extraction operations or provide radiation heating to buildings.
Once the water’s heat is used, it can be returned to the original area to be reheated until it can be reused. It provides substantial cost savings in an eco-friendly manner as it decreases the need to exhaust finite fossil fuels or other non-renewable energy sources to power oil and gas exploration, extraction, and production operations.
The China-based company CNPS is here to help boost efficiency, productivity, safety, and ultimately the profitability of O&G operations by providing high-quality mud logging, enhanced oil refinery, OCTG, oil mining, production, and cementing solutions.
The entire team is dedicated to engineering and promoting more sustainable, advanced, and precise mud logging solutions and geology equipment to maximize this industry’s growth and competitiveness.
Besides mud logging equipment and geological field supplies, they also supply GRE, GRP, RTP, and FRP piping systems, GRE casing solutions, alloy OCTG, and other cutting-edge products to the oil and gas, water, industrial, and marine & offshore sectors worldwide.
Our fiberglass solutions are designed to optimize mud logging equipment longevity, stability, and performance. You can also choose our glass-reinforced piping systems for several other industrial applications.
We cater to a far-reaching, global clientele and have helped numerous businesses achieve compliance, higher performance, and safety standards with our top-notch geological tools and equipment that meet the latest ISO and API standards.
You can set up a consultation with experts at CNPS to streamline the most suitable choice for mud logging solutions or geological supplies for your operations. Alternatively, our representatives are also easily reachable via a quick call.