In the realm of oil and gas extraction, maintaining wellbore integrity is paramount to ensuring the safety, efficiency, and longevity of well operations. Central to this integrity are downhole tubing and casing systems, which serve as essential components in safeguarding the structural integrity of wells.
In this comprehensive exploration, we delve into the critical aspects of wellbore integrity, focusing on the significance of downhole tubing and casing systems in maintaining the structural integrity of wells.
Understanding Wellbore Integrity
Wellbore integrity refers to the ability of a wellbore, the hole drilled into the earth for the extraction of oil and gas, to maintain its structural integrity throughout its operational life. This encompasses various aspects, including preventing fluid migration, ensuring zonal isolation, withstanding downhole pressures, and mitigating the risk of casing failures or leaks. Wellbore integrity is crucial not only for maximizing hydrocarbon recovery but also for protecting the environment and ensuring the safety of personnel and assets,
Role of Downhole Tubing Systems
Downhole tubing systems play a vital role in wellbore integrity by providing a conduit for the production of oil, gas, and other fluids from the reservoir to the surface. Tubing is inserted inside the casing and serves as a primary pathway for hydrocarbon flow. It also allows for injecting fluids, such as water or chemicals, for reservoir management purposes. Tubing must be carefully selected based on factors such as temperature, pressure, corrosion resistance, and mechanical strength to ensure optimal performance and longevity for geological field equipment.
Importance of Casing Systems
Casing systems are integral to wellbore integrity as they provide structural support and prevent the collapse of the wellbore. Casing is installed during the drilling process and serves several critical functions, including preventing formation collapse, controlling formation fluids, isolating productive zones, and providing a conduit for well control operations. Casing must be designed and installed with precision to withstand downhole pressures, temperature variations, and mechanical stresses while maintaining zonal isolation and preventing fluid migration between formations for oilfield service equipment.
Ensuring Zonal Isolation
Zonal isolation, the separation and containment of different geological formations within the wellbore, is essential for maintaining wellbore integrity and preventing fluid migration between formations. Casing and cementing operations are key components of achieving zonal isolation. Casing is installed and cemented in place to create a barrier between formations, preventing the migration of fluids and gases. Proper cementing techniques and quality assurance measures are critical to ensuring effective zonal isolation and minimizing the risk of integrity failures, especially with fiberglass pipes.
Mitigating Casing Failures
Casing failures can have severe consequences for wellbore integrity, including fluid leakage, reservoir damage, and environmental contamination. Various factors can contribute to casing failures, including corrosion, mechanical damage, casing deformation, and cement degradation.
Mitigating the risk of casing failures requires proactive maintenance, inspection, and remediation strategies with the right fiberglass solutions. Advanced inspection technologies, such as electromagnetic inspection and ultrasonic testing, can detect defects and degradation in casing, allowing for timely repairs or replacements to be carried out.
Challenges in Wellbore Integrity
Maintaining wellbore integrity poses several challenges for operators, including complex geology, high-pressure and high-temperature environments, corrosive fluids, and mechanical stresses. In offshore environments, additional challenges such as saltwater corrosion, marine growth, and wellbore stability issues must be addressed. Addressing these challenges requires the adoption of robust design standards, advanced materials, innovative technologies, and comprehensive risk management strategies.
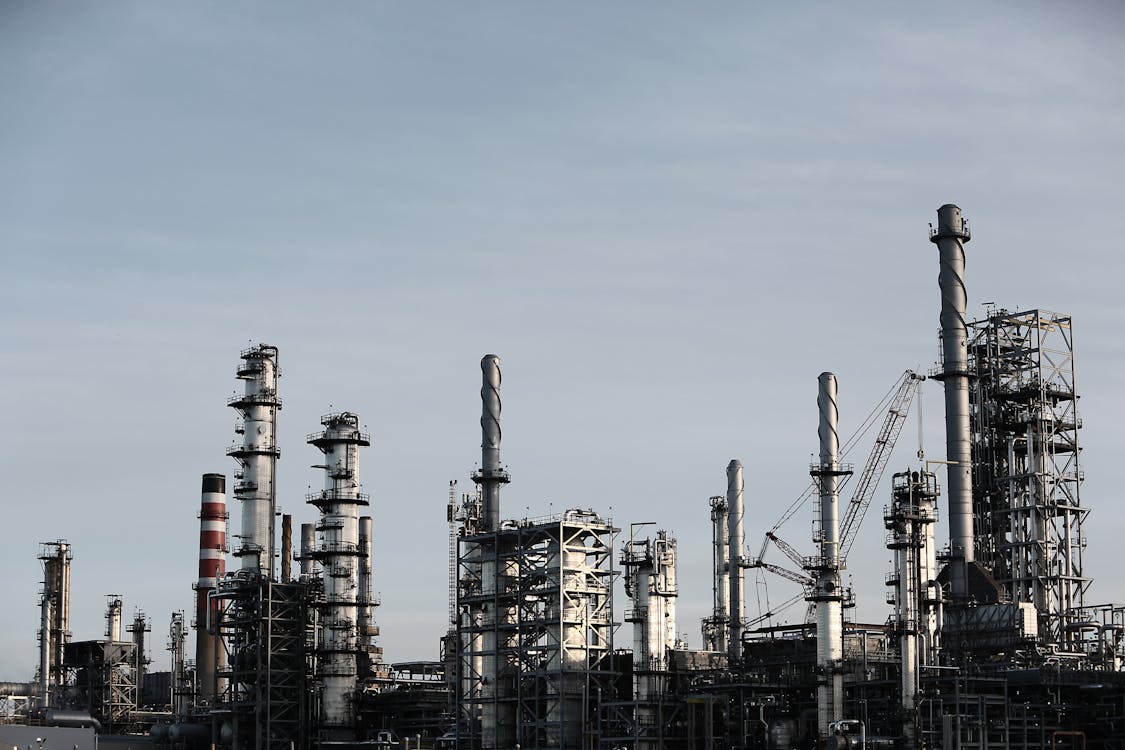
Best Practices for Wellbore Integrity Management
Effective management of wellbore integrity requires a comprehensive approach that encompasses various stages of the well’s lifecycle, from design and construction to operation and maintenance. Implementing best practices ensures the reliability, safety, and efficiency of oil and gas wells. Let’s delve deeper into the key elements of wellbore integrity management.
Rigorous Design and Engineering
Wellbore integrity begins with robust design and engineering based on a thorough analysis of geological data, reservoir characteristics, and operational requirements. Engineering teams must consider factors such as well depth, formation pressure, temperature gradients, and fluid properties to develop well designs that can withstand anticipated downhole conditions. Incorporating advanced modeling and simulation techniques helps optimize casing and cementing designs to achieve zonal isolation and prevent integrity issues for mud logging equipment in particular.
Quality Assurance and Quality Control (QA/QC)
QA/QC measures are critical throughout the drilling, casing, and cementing process to ensure the integrity of downhole tubing and casing systems. This involves stringent adherence to industry standards, specifications, and best practices. Regular inspections, testing, and audits are conducted to verify the quality of materials, equipment, and construction processes. Collaboration between operators, service providers, and regulatory agencies is essential to maintain high standards of quality and compliance.
Regular Inspection, Monitoring, and Testing
Regular inspection, monitoring, and testing of downhole tubing and casing systems are essential for detecting potential integrity issues and ensuring operational reliability. Advanced inspection technologies, including electromagnetic inspection, ultrasonic testing, and acoustic logging, are employed to assess the condition of casing, identify defects, and monitor corrosion rates. Real-time monitoring systems provide continuous data on downhole pressures, temperatures, and fluid dynamics, enabling early detection of anomalies and proactive intervention.
Corrosion Prevention Measures
Corrosion is a common threat to wellbore integrity, particularly in environments with corrosive fluids or high temperatures. Implementing corrosion prevention measures is crucial to mitigate the risk of casing failures and ensure long-term reliability. This may include the use of corrosion-resistant alloys (CRAs) for casing materials, cathodic protection systems, corrosion inhibitors, and coatings. Regular corrosion monitoring and maintenance programs from GRP pipe manufacturers are implemented to assess corrosion rates and address emerging issues promptly.
Proactive Maintenance and Remediation Strategies
Proactive maintenance and remediation strategies are essential for addressing identified integrity issues and preventing unplanned downtime or environmental incidents. This involves developing comprehensive maintenance schedules, conducting routine inspections and testing, and implementing remedial actions as needed. Remediation techniques may include casing repairs, cement squeeze jobs, or corrosion mitigation measures. Well intervention and workover operations are performed as necessary to restore well integrity and optimize production performance.
Continuous Improvement
Continuous improvement is integral to wellbore integrity management, driven by data analysis, lessons learned, and technology innovation. Operators leverage historical data and performance metrics to identify trends, patterns, and areas for improvement. Lessons learned from integrity failures or incidents are incorporated into future well designs, operational procedures, and training programs. Collaboration with industry partners, research institutions, and technology providers fosters innovation and drives advancements in wellbore integrity management practices and technologies.
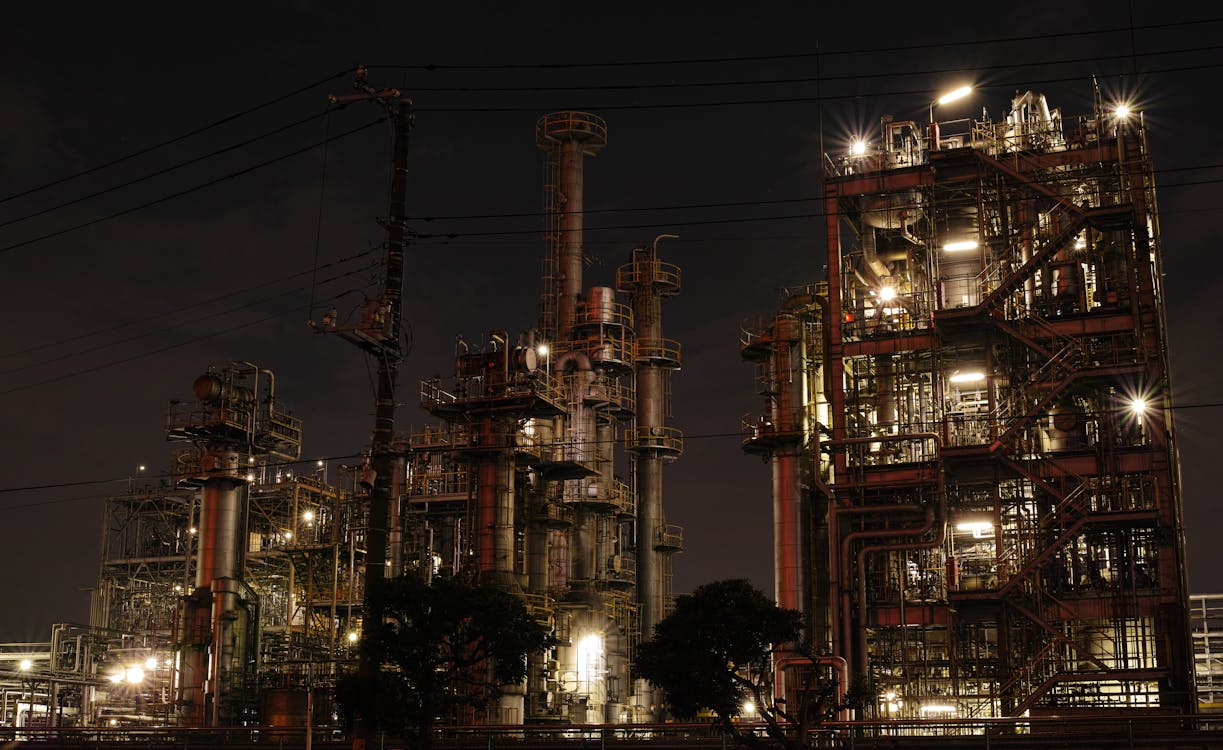
By implementing these best practices, operators can effectively manage wellbore integrity throughout the lifecycle of oil and gas wells, mitigating risks, optimizing performance, and ensuring the long-term viability of their assets. Wellbore integrity management is a dynamic process that requires continuous vigilance, adaptation, and collaboration to meet the evolving challenges of the energy industry.
Common Mistakes in Wellbore Integrity Management
While effective wellbore integrity management is crucial for the success of oil and gas operations, there are several common mistakes that operators may inadvertently make. Identifying and addressing these mistakes is essential to prevent integrity failures, minimize risks, and optimize operational performance. Let’s explore some of the common mistakes in wellbore integrity management:
Inadequate Well Design and Engineering
One of the most critical mistakes in wellbore integrity management is inadequate well design and engineering. This includes insufficient consideration of downhole conditions, formation characteristics, and operational requirements during the planning phase. Poorly designed wells may lack proper zonal isolation, leading to fluid migration, casing failures, and reservoir damage. To mitigate this risk, operators must invest in thorough geological analysis, engineering expertise, and advanced modeling techniques to develop robust well designs that prioritize integrity and reliability.
Lack of Quality Assurance and Quality Control (QA/QC)
Another common mistake is the failure to implement rigorous quality assurance and quality control measures throughout the drilling, casing, and cementing process. Inadequate QA/QC practices can result in the use of substandard materials, improper installation techniques, and non-compliance with industry standards. This increases the likelihood of integrity failures, such as casing leaks, cement channeling, and poor zonal isolation. To avoid these issues, operators must prioritize QA/QC protocols, conduct regular inspections, and ensure adherence to best practices at every stage of well construction.
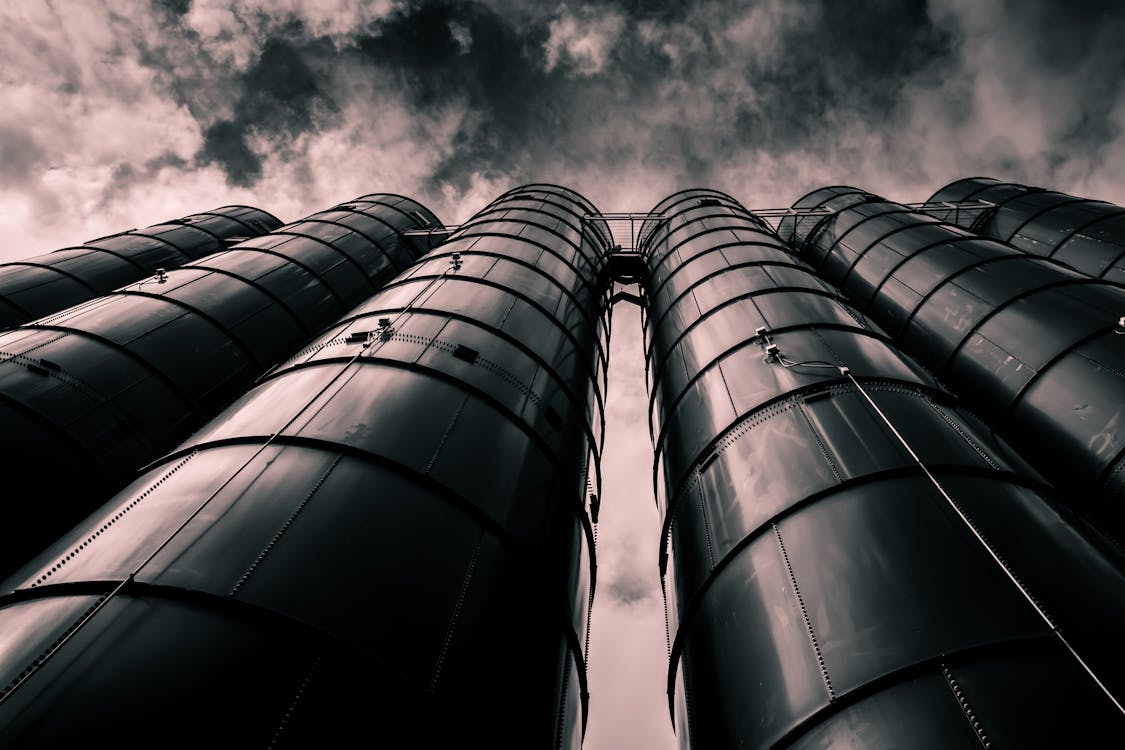
Insufficient Inspection, Monitoring, and Testing
Insufficient inspection, monitoring, and testing of downhole tubing and casing systems is another common mistake that can compromise wellbore integrity. Failure to conduct regular inspections and testing may result in undetected defects, corrosion, or mechanical damage, leading to integrity failures and operational disruptions.
To mitigate this risk, operators should implement comprehensive inspection programs using advanced technologies, such as electromagnetic inspection, ultrasonic testing, and corrosion monitoring. Real-time monitoring systems should be employed to provide continuous data on downhole conditions and performance.
Neglecting Corrosion Prevention Measures
Corrosion is a pervasive threat to wellbore integrity, yet neglecting corrosion prevention measures is a common mistake made by operators. Failure to implement adequate corrosion protection strategies, such as the use of corrosion-resistant alloys, cathodic protection systems, and corrosion inhibitors, can result in accelerated casing degradation and integrity failures. To prevent corrosion-related issues, operators must prioritize corrosion prevention measures, conduct regular monitoring and maintenance, and employ appropriate coatings and inhibitors in corrosive environments.
Conclusion
Downhole tubing and casing systems play a critical role in maintaining structural integrity and ensuring the success of oil and gas wells. Wellbore integrity is essential for maximizing hydrocarbon recovery, protecting the environment, and safeguarding the safety of personnel and assets. By understanding the significance of downhole tubing and casing systems and implementing best practices in wellbore integrity management, operators can mitigate risks, optimize performance, and ensure the long-term viability of their wells in today’s challenging operating environments. The right tools and solutions streamline this process for businesses.
Unlock the power of advanced energy solutions with CNPS! Contact us today for innovative solutions in fiberglass pipes, reinforced thermoplastic pipes, and more.